And their Project finally begins!
Prof. Murugan's pep talk brought a huge difference in the way Pavan used to look at things. Suddenly he realised that there was more than one way of looking at the same thing. He decided he must approach the Inter College project with Kavya from a Growth mindset perspective. He let Prof. Murugan know that he is ready to work on the project. Kavya was ecstatic with Pavan's change of mindset. The two decided to get into a conference call with Prof. Murugan to understand how they should start the project. Prof. Murugan checked with Bharath if he could provide a challenge statement from the industry for the students to get a real exposure.
Pavan and Kavya were very excited about working on this project. But when Bharath shared the problem statement, they both got confused about where should they start from! Bharath asked them to 'improve the purchase experience of the customer in an unmanned electric car showroom'. Perceiving the visible confusion on Kavya and Pavan's face, Prof. Murugan and Bharath promised to provide them the guidance they will require throughout the course of the project. Prof. Murugan asked them to schedule bi-weekly calls with him to discuss the progress of the project.
In the first call, Prof. Murugan asked Pavan to create the initial plan based on the discussions they had on project management before. He told Kavya and Pavan, "When you get a defined problem statement like in this case, you should always start with identifying the one for whom you are creating value"
An excited Kavya replied, "In this case it is the electric vehicle buyer."
"Absolutely correct! Now you need to provide this buyer value by improving the in-showroom experience." said Prof. Murugan
"That too when the showroom is unmanned" replied Pavan.
"Well, at this point, you need not worry about it. First start with the value creation part which is improving the in-showroom experience for an electric car customer. The 'unmanned' part has more to do with the technology, which we will consider while developing our solution"
Prof. Murugan asked them to do customer research and understand more about the in-showroom experience of car buyers. Kavya and Pavan had a chat and they decided to individually run customer research, collect as much data as possible and then discuss over a call to synthesize. They searched a lot on internet but hardly could find anything satisfactory. They had to advance their meeting to discuss a better strategy. Kavya suggested that both of them know someone or the other owning a car and they should send these people a Google form with few questions to get their views about in-showroom experience. This time there was some 'success'. People did fill the forms but most of the things that they talked about were either very vague or were not just good enough. Both Pavan and Kavya got very disheartened with this result. They expected to share some crucial insights with Prof. Murugan when they met him the next meeting.
Prof. Murugan, however, was not at all surprised with the result. He told them, in order to get valuable insights one must dig into an user's experience much like how that individual felt. This is called being empathetic. Sharing a Google form with some questions and asking the user to answer those, most of the time, does not help in feeling empathy for the user. By this, very critical aspects tend to get missed out. These critical points often include the facial expressions made; the words being used while explaining an experience etc. While describing their experience in writing, these factors get highly suppressed by users. It is thus important that Pavan and Kavya try to conduct in-person interviews. Kavya was worried about the current pandemic situation and how easy it will be to meet someone. Prof. Murugan suggested that they do online interviews of chosen users.
Pavan felt very excited with the thought of conducting these in-person interviews. He said that they may provide small saplings as gifts for those who agree to participate in the interviews. Prof. Murugan interrupted him and said, "That is a very good thought, Pavan. Giving a gift always incentivises people to participate more in such type of activities. However, I am curious about why you want to give them saplings as gift?"
"I was planning to interview some electric vehicle car owners and I think because they are environment conscious, they might like my gift" justified Pavan.
"Thanks for bringing this up, Pavan. But this is one mistake we make most of the time when we do customer research. And it is called a bias."
Both Pavan and Kavya looked at each other confused thinking what is this bias and what it has to do with the saplings! Bias is a preconceived notion about something without verifying it with primary research or first-hand information. Pavan and Kavya decided to visit an automotive dealer shop in their respective towns to understand what customers looked for.
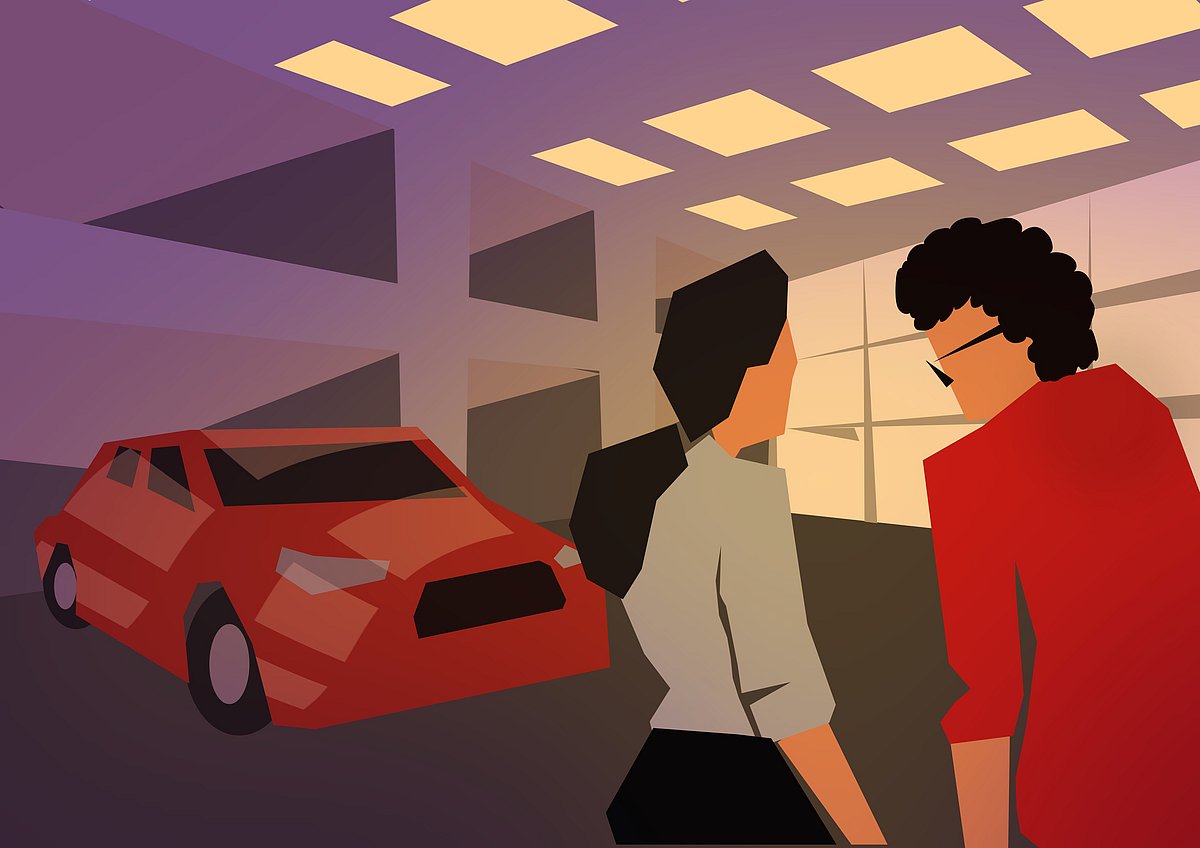
Nepal baby warmer example
An insightful example to appreciate the importance of empathy in designing a product is the baby warmer example. The “Design for extreme affordability” group at Stanford University, as part of their project Embrace, studied the high infant mortality among premature babies. The team took up Kathmandu, Nepal as the experimental site. Initially, they came up with an expensive incubator to keep the preterm babies warm in the hospital. But the mortality rate did not come down at all.
When they went out into the field to study the cause of failure, they realized that most of these babies were living in remote rural regions. Their mothers had a challenge in keeping them warm when bringing them from homes that were far away from the doctor. What was needed was a low cost and portable baby warmer that could work in rural environments, without electricity. The team came up with a product that looked like a sleeping bag. It can be used to wrap the babies. A wax type of phase change material (PCM) was used to fill the sleeping bag. It could be heated using boiling water. It stayed warm for four hours. This became a popular product that met its purpose. The Embrace team had to empathize with the mothers and babies to truly understand what they underwent and then come up with a solution- that works well despite the infrastructural constraints.
Tata Nano example
Another insightful case in designing affordable products for customers in emerging markets comes from the Tata Nano story. Mr. Ratan Tata had noble intentions when he came up with a vision for an affordable car, for the middleclass segment in India. In his own words, a father riding a scooter with his wife sitting behind him and a child standing in front was an unsafe situation. That is when he wanted to come up with a car at a price of Rs. 1 lakh, making it affordable for the large middleclass segment. The car was launched in 2008. But the volume of sales never picked up to the levels the management expected. The car was eventually abandoned in 2018.
It was not the technology behind the Nano that led to its failure to take off. It was the way its targeted customers and their needs and perspective was understood. Several experts have written about the Nano story. Cars are also a status symbol. So it was not just the price of the car or its mileage but other softer aspects too that mattered. The marketing team and the media branded the car as “the cheapest car”, and that did not go well with potential customers. However good the intentions and the technology behind the launch of a new product, understanding the needs and sentiments of the end users, through a first-hand experience, is key to the product’s success. Here the mobility engineer while practising empathy, looks beyond the rational need of the customer but also at their emotional needs.
Drive-by-wire technology
As part of his usual technical mentoring sessions, Bharath called Pavan one day to describe to him drive-by-wire, also called "x-by-wire" that is fundamentally changing the way we drive. Bharath likes to walk while talking, so they went for a long walk as they talked about the technology. A car’s drive-by-wire relies mainly on electronics to control a wide range of vehicle operations, including acceleration, braking and steering. Conventional cars use hydraulic and mechanical technology to conduct these same basic operations, and although the systems are powerful, they can be overly complex, inefficient and subject to wear and tear over the years. Drive by wire technology brings many advantages to electric, autonomous and connected vehicles.
This technology replaces the traditional mechanical control systems with electronic control systems. It uses electromechanical actuators and human-machine interfaces such as pedal and steering feel emulators. Components such as the steering column, intermediate shafts, pumps, hoses, belts, coolers and vacuum servos and master cylinders are eliminated from the vehicle. This technology has been adapted from the fly-by-wire systems used widely in the aviation industry since the 1990s. By-wire systems began to be installed about twenty-five years ago, first in the military, and later in commercial aircraft. In the 1970s, NASA developed fly-by-wire technology to manoeuvre the Apollo Lunar Module [3-6] [9].
By replacing conventional throttle systems, drive-by-wire systems can significantly reduce the number of moving parts. This reduces weight, increases operational accuracy, and stretches out the time between service visits for maintenance and other adjustments. Less weight and better accuracy would equal better fuel efficiency and fewer emissions too. The electronic throttle system is significantly lighter and using a control system, allows precise control of the throttle opening. Since the steering wheel can be bypassed as an input device, safety can be improved by providing computer controlled intervention of vehicle controls with systems such as electronic stability control (ESC), adaptive cruise control and Lane Assist Systems. The only concern has been that these Drive by wire systems can be "hacked", and their control faulted or shut off, by either wired or wireless connections [3-6].
Throttle-by-wire, or accelerate-by-wire, was the first type of drive-by-wire system to be introduced. This system helps accomplish vehicle propulsion by means of an electronic throttle without any cables from the accelerator pedal to the throttle valve of the engine. In electric vehicles, this system controls the electric motors by sensing the accelerator pedal input and sending commands to the power inverter modules. These systems use a pedal unit and an engine management system. The pedal uses sensors that measure how much or how little the driver moves the accelerator, and the sensors send that information to the engine management system. The engine management system is a computer that determines how much fuel is required, and it provides this input to an actuator. The pedal could be the same one drivers have become accustomed to using today, an easy-to-reach pad placed near the foot that's pressed down in order to accelerate the car. This is often seen as the safest type of drive-by-wire technology, as it is easy to implement with a fool-proof, fail-safe design [3-6] .
Brake by wire - Traditional hydraulic brakes make use of a master cylinder, as well as several slave cylinders. When the driver pushes on the brake pedal, it applies physical pressure to the master cylinder. In most cases, that pressure is amplified by a vacuum or hydraulic brake booster. The pressure is then transmitted via brake lines to the brake calipers or wheel cylinders. Anti-lock brake systems were early precursors of modern brake-by-wire technologies, in that they allowed the brakes of a vehicle to be pulled automatically with no driver input. This is accomplished by an electronic actuator that activates the existing hydraulic brakes. Other safety technologies have been built on this foundation [3-6].
Electronic stability control, traction control, and automatic braking systems depend on ABS and are peripherally related to brake-by-wire technology. A pure brake by wire system would eliminate the need for hydraulics completely by using motors to actuate calipers, in comparison to the current technology where the system is designed to provide braking effort by building hydraulic pressure in the brake lines. There are two types of brake-by-wire systems : (a) Hydraulic, or "wet," brake-by-wire uses additional hydraulic parts to create pressure on the brakes and (b) Electric, or "dry," brake-by-wire, on the other hand, simply uses an electric motor and no hydraulic brake fluid [3-6].
Also Read: Mobility Engineer 2030: Having a Growth Mindset is Key to Success!
Shift by wire - the direction of motion of the vehicle (forward, reverse) is set by commanding the actuators inside the transmission through electronic commands based on the current input from the driver (park, reverse, neutral or drive). Steer by wire - this kind of system will provide steering control to a car with fewer mechanical components / linkages between the steering wheel and the wheels. The control of the wheels' direction will be established through electric motor(s) which are actuated by electronic control units monitoring the steering wheel inputs from the driver. Sensors detect the movements of the steering wheel and send information to a microprocessor. The computer then sends commands to actuators on the axles, which turn according to the driver's directions. Park by wire - the parking pawl in a traditional automatic transmission has a mechanical link to the gear lever and locks the transmission in the park position when the vehicle is set in Park. A park by wire system uses electronic commands to actuate the parking pawl by a motor when the driver puts the vehicle in park.
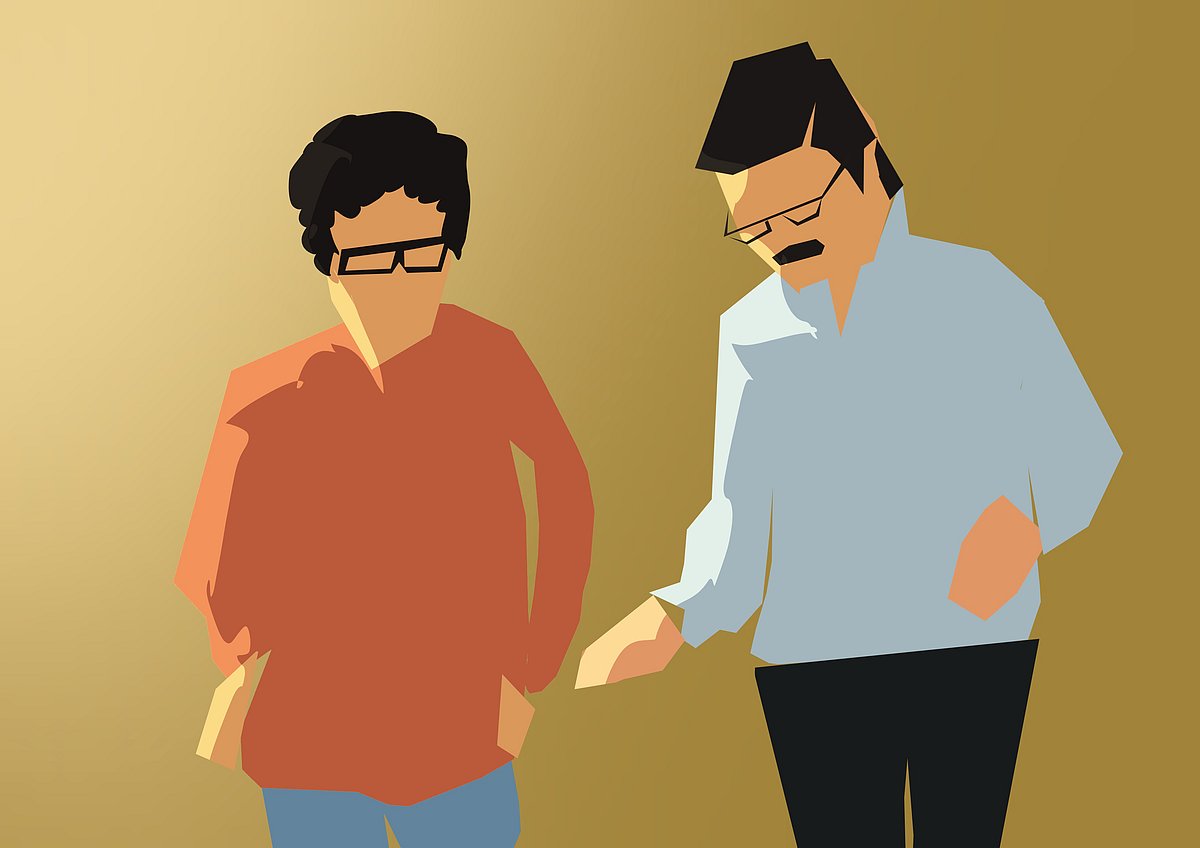
Bharath wrapped up the discussion by emphasising how the drive by wire market is projected to reach USD 31.9 billion by 2025 from an estimated USD 24.0 billion in 2020 at a CAGR of 5.9% during the forecast period. [8] The major driving factor is the increasing number of mandates by governments to control vehicle emissions and the demand for passenger comfort. The drive by wire technology helps in achieving that by reducing the weight of the vehicle, and thus, increasing fuel efficiency [8]. Pavan had to now think of ideas of how he could use drive-by-wire technology in his project to meet customer needs.
Note: All opinions and points-of-view expressed above are those of the authors and do not represent that of any other individual or organization.
References
1 - Embrace, Extreme – Design for extreme affordability, Stanford University
2 – Learning from Tata Nano’s mistakes, Matt Eyring, January 11, 2011, Harvard Business Review
3 – Drive by wire, Wikipedia
4 – How drive-by-wire technology works, John Fuller, How Stuff Works
5 – What is drive-by-wire technology, Jeremy Laukkonen, July 16, 2021, Lifewire
6 - The coming revolution of drive-by-wire cars - https://www.youtube.com/watch?v=vlM-VcQVMo0
7 - Drive by Wire - https://cecas.clemson.edu/cvel/auto/AuE835_Projects_2009/pillai_project.html
8 – Drive by wire market by application, Markets and Markets
9 – Driving by wire, National Museum of American History
Connect with Authors on LinkedIn:
Dr Shankar Venugopal | Ramachandran S | Sayantan Mukherjee
source https://www.vikatan.com/automobile/motor/mobility-engineer-2030-part-10-empathy-as-a-core-skill-for-mobility-engineers
கருத்துகள் இல்லை:
கருத்துரையிடுக